Category Archives: Industry News
Pvc shrink film application
In the 21st century, the rapid development of plastic film, Pvc shrink film applications are increasing, including agricultural greenhouses, as well as product packaging, etc., the reason why it can be so widely used, its main reason is to have the following advantages:
Wrapping and packaging the goods stacked on the pallets to make the package more stable and tidy, and more super waterproof;
High tensile strength, high elongation, good self-adhesion, high transparency;
Shrink film, heat shrink film is mainly composed of several different brands of polyene resin mixed extrusion, with puncture resistance, high strength and high performance;
Heat Shrink Film Touch Film Technology mainly refers to some major steps in the production of heat shrink film blown film, such as extrusion, forming, cooling, traction and winding heat shrink film. When the number is doubled, the area of heat absorption is large, and the plasticization effect is good. Naturally, it will increase the output, supplemented by the improvement of cooling technology, and the output can be increased by 50%.
PVC shrink film has some deficiencies. For example, some PVC heat-shrinkable films are very soft when used in the summer and harden as soon as they reach winter; some heat-shrinkable films easily absorb dust and become opaque; some PVC heat-shrinkable films have a short service life and are prone to ageing. Wind and sun exposure, the surface is easily cracked. The application of PVC heat shrinkable film is still very extensive. It is believed that as the technology of heat shrinkable film becomes more and more mature, the heat shrinkable film will be applied in more fields.
Main technical indicators of white masterbatch
The production of protective film is inseparable from the plastic masterbatch. Today we will talk about the most commonly used plastic masterbatch in the production of protective film: white masterbatch has bright color, bright and eye-catching, high color strength, good dispersion, high concentration, It is widely used in injection molding, blow molding, wire drawing, casting, extrusion, blown film, foaming, sheet, pipe, pumping, etc., with good whiteness, strong hiding power, good migration resistance and heat resistance. Hollow, EVA, blown bottles, sheets, household appliances, toys, packaging materials, wires and cables, plastic bags, automobiles, building materials, sports and leisure products, packaging bags, packaging bottles and other plastic products industry.
Main technical indicators of white masterbatch
1, resistance to migration (grade) [≥ 4]
2, the moisture content (%) [≤ 0.30] 8, the total color difference [≤ 1.50]
3, melting temperature (oC) [125 ~ 200]
4, white masterbatch dispersibility: [colorless dots, stripes]
5, lightfastness (level) [5-8]
6, white masterbatch appearance granular, uniform particles, uniform color
7, heat resistance (grade) [≥4]
In theory, the white masterbatch that meets the above technical specifications is of good quality.
10 aspects to consider when choosing a white masterbatch
1, whiteness
The whiteness of the white masterbatch is mainly represented by the titanium dioxide in the masterbatch. There are many factors that affect the whiteness of titanium dioxide, including the size, shape and size distribution of titanium dioxide particles, the type and content of impurities, and the lattice of titanium dioxide particles. Defects. In general, since the chlorination method has high purity of titanium dioxide as a raw material and less impurities in the preparation process, the whiteness of the chlorination titanium dioxide is better than that of the sulfuric acid method. In the actual white mother market, many white masterbatch manufacturers impersonate titanium dioxide by adding equal amounts of calcium carbonate, barium sulfate, and zinc sulfide. In fact, the whiteness of these inorganic powders is incomparable with titanium dioxide. .
2, hiding power
Hiding power is also a very important indicator of white masterbatch. Good hiding power means that the pigment has strong coloring ability, and the desired effect can be obtained with a small amount of additive. The hiding power of the white masterbatch depends on the choice of titanium dioxide. Compared with the processing technology, rutile titanium dioxide has a smaller and tighter unit lattice and a larger refractive index than rutile titanium dioxide, so the hiding power and anti-ultraviolet light performance are obviously better than anatase. For the same type of rutile titanium dioxide white masterbatch, titanium dioxide particle size is small, narrow particle size distribution, good hiding power in the masterbatch is significantly larger than the titanium dioxide particle size distribution, poor performance in the masterbatch it is good. Similarly, the common hiding power of calcium carbonate, barium sulfate, and zinc sulfide is not comparable to titanium dioxide.
Table 1 Refractive index of different substances
From the above comparison of the refractive index, it can be known that the refractive index difference between the rutile titanium dioxide and the carrier PE resin is the largest, and the dispersion effect is the best, and the hiding power is the strongest.
3, dispersion
Dispersibility has an important influence on the application of titanium dioxide in plastics. In general, the finer the titanium dioxide particles, the better the dispersion, the higher the strength of the tinctorial force, and the fine dispersion of the white masterbatch when the film needs to be finely printed. Grain pattern clarity, layering, and vividness are better because the microscopic smoothness of the base film is one of the determinants of the quality of the printed pattern.
4, moisture content
The moisture content of the white masterbatch also plays an important role in the performance of the masterbatch. In general, the moisture content should be controlled below 1500ppm, and the strict requirements should be below 600ppm. In the injection molding process, the raw materials are generally dried before production. In the production of thin films, customers buy directly after being premixed with the carrier. If the moisture content of the masterbatch is high, it will directly lead to film rupture, and there will be small bubbles formed on the film, “crystal point”. Defects, and cause the high moisture content of white masterbatch from the raw material used in the masterbatch to the process have an impact.
5, smell
Some film manufacturers will smell a strange odor after using white masterbatch, which is absolutely not allowed in the milk film and film that comes into contact with food. This is mainly due to the fact that the titanium dioxide in the masterbatch is organic. During the treatment process, the coating auxiliaries selected are not suitable or the amount added is too large, or there is a problem with the dispersant used in the production process of the masterbatch, and the white masterbatch grade can be replaced.
6, Hue selection
Due to the low reflectivity of the rutile titanium dioxide in the violet region, the rutile titanium dioxide has a “yellowish” color tone, and the “yellowish” color tone will give the colored product a “stale” feeling and will make the fine print image vivid. Decrease in the degree and layering, which is unwelcome among many white masterbatch users, but after adding a trace of fluorescent whitening agent to titanium dioxide, it can absorb ultraviolet light with a wavelength of 300-400nm and convert it to a wavelength of 400 – 500nm blue fluorescence, so that white masterbatch was “blue phase”, white masterbatch users according to their needs.
7, liquidity
The fluidity of the white masterbatch can be expressed as the melt index (MI), low numerical flow, high numerical fluidity, good fluidity means good processing performance, low machine torque, low power consumption, and the user selects white masterbatch In addition to requiring the masterbatch to have good fluidity, it is also important to note that the masterbatch should be compatible with the carrier resin in its own factory product. The general principle is that the MI of the masterbatch should be higher than that of the carrier resin.
8, printing heat sealing performance
White film products require printing and heat sealing in most cases. Addition of calcium carbonate in the white masterbatch can affect the sharpness and vividness of the printed pattern. Incorrect or excessive amount of dispersant added to the masterbatch can also affect the heat seal and Printing performance.
9, lightfastness and weatherability
White masterbatch generally requires lightfastness of 7-8 grades, weather resistance of 4-5, and temperature resistance of 280 degrees. These requirements mainly depend on the quality of titanium dioxide. To achieve the above conditions, it must be rutile titanium dioxide. .
10, RoHS & FDA
Heavy metal detection and food contact permitting are also important indicators for white masterbatch, because many white films are used in food packaging. Passing FDA food certification is a test that must be passed.
Precautions when using white masterbatch
1, in order to reduce the color after the fiber color difference, the white masterbatch should be diluted to control the mixing ratio, filaments not less than 3% to 10%, staple fiber not less than 1% to 3%, monochrome monofilament continuous filament Spinning with three-color equipment, the white masterbatch must be fed into the extruder after mixing. At the same time, to increase the mixing capacity of the melt itself, a mixing device can be added to the extruder section.
2. White masterbatch mixing method After the color silk color formula is determined, the white masterbatch is evenly dispersed in the polypropylene slice before spinning, which is the key to ensure the product quality. There are two specific mixing methods. One is the heavy method and volume method. After the white masterbatch is melted in the extruder or at the back, it is injected into the polypropylene melt with a small extruder, and the uniformity is very good.
3. When choosing the white masterbatch, choose according to the selection range. The polypropylene masterbatch has the fine denier grade and the coarse denier grade. The coarse masterbatch white masterbatch color can not be used for fine denier grades, and the color should be considered when spinning For the denier of the monofilament of the fiber, the same level of white masterbatch was selected.
4, the choice of white masterbatch is preferably the same manufacturer’s products, in order to reduce costs should be selected high concentration white masterbatch. Pigments for white masterbatch have high, middle and low grades. When matching colors, white masterbatch of different grades should be properly selected according to the quality requirements of the fiber. In order to avoid the quality variation of the finished fiber caused by the different light and thermal stability of the pigment, the color of the white masterbatch that meets the fiber quality requirements and has the same level of light and heat stability should also be selected.
The feature and uses of PE blue film
PE Blue Film Features
Protective film is used by everyone, but few people really understand its features and functions. The blue PE protective film is generally divided into two types, one is a hydrogel PE blue protective film and the other is an oil gel PE blue protective film. Let’s focus on the blue PE protective film.
PE blue film is produced by adding blue pigment to the transparent film in the process of blown film, and then it is produced by coating technology and coated with oily glue or water-based glue. It is generally divided into two types, one is a hydrogel PE blue protective film, and the other is a PE gel blue protective film. The blue PE protective film inherits the performance of the PE protective film. The blue PE protective film uses a special polyethylene (PE) plastic film as the substrate. According to the density, it is divided into high-density polyethylene protective film, medium-density polyethylene, and low. Density polyethylene.
The biggest feature of PE blue film is blue, why should it be made blue? This is determined by the market and the user’s preferences. In the long-term use of the protective film, in the market with some special products, the blue protective film is much better than the transparent protective film, and it is easy to identify. Some products, after being attached with a transparent protective film, can not tell where the film is. This will lead workers to make it difficult to remove the transparent protective film and reduce the production efficiency. However, the blue PE protective film is a good solution to this problem. Another feature of the blue PE protective film is to cover the defects of the product and prevent the product from affecting sales due to defects.
The main purpose of PE blue film
1, computer hardware products: computer chassis shell, galvanized sheet stamping, computer paint board, plastic injection molding, printing and painting parts surface protection.
2, liquid crystal photoelectric series: LCD liquid crystal display, backlight, EL electroluminescent film, conductive membrane switch, touch screen, color computer monitor surface protection.
3, plastic injection products: ABS, PP injection products, PVC sheet, acrylic panels, dashboards, plastic lenses.
4, brand-name printing: PVC, PC, aluminum, copper and other metal, plastic brand name surface protection.
5, decorative sheet: stainless steel, aluminum alloy, aluminum curtain wall, titanium plate, plastic steel plate, Polaroid plate, ceramic, polyester sheet and other products surface protection.
6, clean room series: sticky floor rubber, sticky roller, anti-static bags and other products.
In summary, the PE blue film not only helps the articles to isolate the air pollution, but also protects the articles themselves, and can effectively prevent the articles from being scratched or scratched.
Protective film performance and use requirements
The continuous development of the society and the progress of mankind, its people’s requirements for the quality of life are constantly improving, and its various new things are constantly emerging. It is this kind of seemingly ordinary life that has brought great convenience to us. In traditional packaging, the amount used by our food industry and medical industry is very large. Past use of packaging is a very serious environmental pollution.
Protective film performance requirements
1. The protective film is inert to the surface of the material being protected.
2. When the protective film is used, the material to be protected will have good adhesion properties to some extent. During the handling and processing of the material, the protective film will not warp or fall off.
3. The protective film has good weather resistance and stability of holding strength to a certain extent. After a few days or a long time, the peeling force does not increase significantly, and it is easy to peel off. When it is removed, there is no residue on the protected surface. The glue remains, no pictures.
4. Low crystal point.
Protective film requirements
1. Suitable for stickiness: easy to paste and easy to tear.
2. The peeling force is stable, and its change is small when it is operated, that is, the smaller the peeling force rises, the better.
3. Weather resistance is good, under sunlight exposure conditions, the use period of up to six months to one year.
4. Long storage period, more than one year in the warehouse, no change in quality.
5. No pollution, no corrosion, the adhesive is inert and does not react chemically with the surface of the adhered material.
6. Excellent mechanical properties, in line with user requirements of tensile strength, elastic modulus, elongation and so on.
PE protective film suitable for stickiness and production principle
PE protective film has become more and more useful in the process of its use, and its variety can be seen in various forms in the market. The greatest strength of PE protective film is that the product being protected is produced and processed in PE protective film and transported. During the storage and use, it will not be polluted, corroded, scratched, maintain the original bright and shiny surface, and then improve the quality and market competitiveness of the product.
PE protective film suitable for stickiness
1.PE protective film easy to paste easily tear.
2. Long storage period: more than one year in the warehouse, no change in quality.
3. Peeling force stability: little change over time, ie, the smaller the increase in peel force, the better.
4. Good weather resistance: under sunlight exposure conditions, the use period is up to six months to one year.
5. No pollution, no corrosion: The adhesive is inert and does not chemically react with the surface of the adhered material.
6. Excellent mechanical properties: Meet the user requirements of tensile strength, elastic modulus, elongation and so on.+
PE protective film production principle
1.PE protective film adhesive (glue) has a viscoelastic polymer, film, tear film.
2. The main factors affecting the viscosity: wetting, penetration.
PE Protective Film Adhesive (Glue) Has Viscoelastic Polymer
Film: The adhesive layer can be in close contact with the surface of the adherend and flow into the groove of the adhered surface as much as possible, so that the effective contact area increases.
Main factors affecting stickiness
Wetting: The pressure-sensitive adhesive can achieve close contact only with good wetting of the surface of the adhered object, creating conditions for physical and chemical bonding to move and diffuse the molecules: The pressure-sensitive adhesive molecules will move to the surface of the adhered material when the two are When the distance between the bond is less than 5A, physical and chemical bonding will occur.
Protective film should be used gently
In the use of plastic sheet protective film, the correct steps should be taken, because the protective film material is thin, improper use of the protective film is easy to damage, how to use to make the protective film has a good full performance?
Plastic sheet protective film recommended sticking method:
First: The width of the protective film is varied. From 7CM-130cm, but no matter how wide the protective film is used, it should be evenly and forcefully pulled apart in parallel, and the speed should be uniform. This will prevent the protective film from being unevenly pulled by the force when the protective film is torn to protect it. The surface of the film may have uneven thickness, resulting in an edge warping, or a decrease in the viscosity of the adhesive.
Second, gently stick it on the plastic sheet, tear the edges, and don’t tear too much. This prevents the dust in the production plant from sticking to the glue in the process of adhering and reduces the stickiness of the glue, and the protective effect and the transparency effect are deteriorated. The same will also prevent tearing too much, the paste is not timely, the membrane and the film paste, there wrinkles, affecting the appearance and effect, paste on the sheet after lightly paste, moderate strength, not too much.
Difference between PE protective film, PET protective film and PVC protective film
PE: Polyethylene, widely used in the protective film industry
Its main features are: low price, softness, good extensibility, no environmental pollution, and generally such products have passed the EU’s ROHS environmental pollution test.
Disadvantages: poor weather resistance, this material is not suitable for use at high temperatures, generally within 60 degrees.
PVC: polyvinyl chloride
Its characteristics are: good flexibility, weather resistance (SPVC).
Disadvantages: Not environmentally friendly, so many international brands rarely use this material. This product is mainly used for anti-static protection more, there are wooden speaker surface.
PET: Polyester
Its main features: good weather resistance, can withstand 100-150 degrees high temperature, good hardness, smooth.
Disadvantages: Cannot be used on angled or corner products. The main use die cutting.
Global protective film consumption exceeds 5 million tons per year
PE protective film It is a special polyethylene (PE) plastic film as the substrate protective film, with protection products in the production process, transportation, storage and use of the process will not be contaminated, corrosion, scratches and other injuries, so that the product surface Maintaining the advantages of smoothness, glossiness, and other advantages can improve the quality of products and their competitiveness in the market.
Due to the clear glossy surface protection and low price, PE protective film has achieved unprecedented success in the packaging market in the past 30 years. It not only succeeded in replacing cellophane but also rapidly developed its own market. Composite film replaces paper. At present, the global protective film consumption exceeds 5 million tons per year and is growing rapidly.
With the development of China’s PE protective film production technology, a large number of excellent PE protective film manufacturers emerged, and quickly transformed our country from a net importer of protective film to a net exporter, making a huge contribution to China’s economic development. contribution.
It is reported that Asia is the fastest growing market for PE protective film, and the industry has good prospects for development.
PE protective film material and use and how to choose

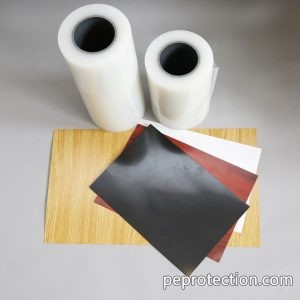
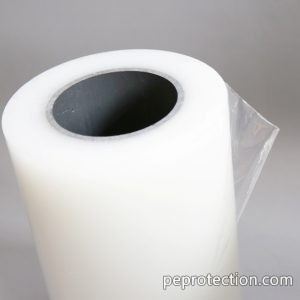
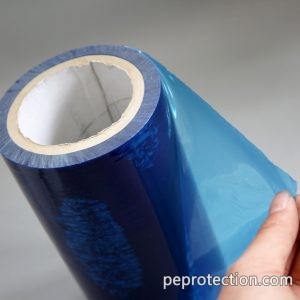
Recognizing the Women in the Window Film Industry
March 8th marks International Women’s Day, an annual worldwide celebration of women’s achievements. In honor of this, Window Film magazine spoke to numerous female dealers, installers, CEOs and product specialists from the window film, paint protection film (PPF) and vinyl industries to recognize their personal and professional endeavors.
They may have landed in the business by accident, but they’re here and paving the way for future generations of women to find opportunity in this male-dominated industry. Get to know just a few of these amazing women below, whom we asked about their journey to and through the industry, as well as questions about their life outside of their careers. For the full article, look to the March/April issue of Window Film magazine.
Carole Lockwood
What attracted you to the window film industry?
“Learning a new skill provided me an opportunity to support myself and my family. It was fun and challenging. I could meet new people, learn new skills and have flexible hours. It’s a great lifestyle … opened a whole new world to me. I found I really loved my job.” –Carole Lockwood, owner, The Tint Shop Texas, Tyler, Texas
If you weren’t doing this job, what would you be doing?
“Probably selling trucks. I had a short stint selling them for 10 months, and I loved it. That’s why I wanted a product to sell to that market.” –Maddison Lawrence, owner, Slick Azz Protective Coatings, Brisbane, Australia
Maddison Lawrence
“Finishing training as a makeup artist.” –Lindsay Webdell, channel market manager – Americas, Saint-Gobain Solar Gard, San Diego
What’s something about you no one knows?
“I have a dream to be an astronaut. I want to see and view the Earth from outer space.” –Saisamorn Channapa, managing director, Techno-Sell (Frey) Co., Ltd, Bangkok, Thailand
“I like flowers and classical music.” –Sharon Bronson, owner, DarthShader Tint & Vinyl, Orlando
“As a young child (I would guess around 5 years old) growing up in a suburb of Seattle, I became fascinated (obsessed) with the idea of having a pet cow. My older sister and mother would ask me tough questions: ‘Where would the cow live?’ to which I had to think carefully. Where would my pet cow live? At the time, ‘in my room’ seemed like a perfectly appropriate answer. As an adult looking back on this, I realize this was the beginning of my having to think outside of the box for how I could tackle future big challenges.” –Katherine Becher, owner and creative director, Wicked Wraps, Mukilteo, Wash.
Tamara Baumann
“I don’t really like being the center of attention. I seem flashy and loud with the way I carry myself sometimes, but, in all honesty, I like to be behind the scenes making things happen much more than I like being out on the front lines. I like to direct and be in charge, but I can be somewhat introverted from time to time and enjoy being a home body.” –Tamara Baumann, owner, UnderWraps, Huntington Beach, Calf.
“I drive a vintage midget race car with my dad. We are in a car club where we actually get to race these old cars in exhibition type races. For those into sprint car racing, I have even raced at the legendary Knoxville Raceway in Knoxville, Iowa and was lucky enough to meet ‘Cappy’ Capitani on several occasions. I am one of only two or three women drivers in the club. The rest of the club is a bunch of ‘old guys’ like my dad, and they welcome me with open arms and we have a great time.” –Molly Waters, senior technical specialist, Avery Dennison, Dallas
“I’m a Yankee Doodle sweetheart, born on the Fourth of July. I have an identical twin sister, Cindy (yes, there’s two of me). My twin sister and I had our baby girls on the exact same day—just 12 hours apart.” –Sylvia C. Meza, regional sales manager, Reflek Technologies, Long Beach, Calif.
Carol Borow
What’s the best advice you’ve ever gotten?
“I took a public speaking course while in school. Part of the assignment was to make an outline of the speech and then present it. I went up to the podium and gave my speech. Guess I didn’t hear the part about the outline. Well, the teacher yelled at me, embarrassed me in front of the class. I went home and literally wanted my dad to harm this teacher. At that point, my father gave me advice that I still value. He told me to tell the teacher that I had made an error, but he had no right to embarrass me. My father said, ‘Stick up for yourself, and don’t let people step on you. Stand tall and believe in yourself. You can’t rely on others to fight your battles.’
So, I told the teacher, ‘I made a mistake, but you shouldn’t have embarrassed me in front of the class. Don’t ever speak to me like that again.’ I said it in a calm and respectful manner. I remember that lesson pretty much every day.” –Carol Borow, president, CHB Industries, Smithtown, N.Y.